10年越しのコンプレッサー “大型”省エネ実現
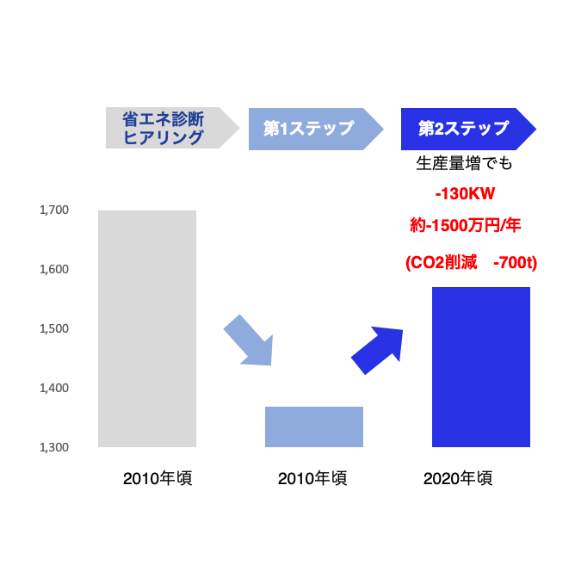
弊社ではコンプレッサーの省エネ診断を行っており、データ測定を実施して最適なコンプレッサーやコンプレッサー周辺機器のご提案・設置工事・メンテナンスを行っております。
今回は、約10年越しで実らせたコンプレッサーの省エネの事例をご紹介させていただきます。
省エネ診断で -1500万円/年 脱炭素-700t/年
「また、電気料金減ったぞ」
ある日、お客様から嬉しそうな電話が届きました。
少し前にコンプレッサーを導入し、その後しっかり電気料金が下がった為です。本当に嬉しいですね。
10年ほど前「コンプレッサーとドライヤーがどうしようもない。何とかしたい。」というご相談を受けたのが始まりです。
コンプレッサーの省エネ診断(データ測定)と現場調査を行うと、
・エアーを無意味に捨てていた
・ドライヤーのトラブルで、頻繫に生産が止まっていた
・コンプレッサーの圧力は特に設定しておらず、高いままにしてある
などなど、たくさんのムダと困り事を抱えている事が分かりました。
調査結果をふまえて、コンプレッサーだけでなく、ドライヤーや配管、タンク等、すべての過程において提案をし、併せて配置図面を作成しました。
一気に投資ができないので、2つのステップに分けて設備投資を行うことになりました。
ステップ1
250kWコンプレッサ×3台と、ドライヤー×2台を導入し低圧化させることで、電気量-330kWを実現しました。
その後は弊社がメンテナンスを行い、ドライヤーのトラブルやコンプレッサーが停止することはなく、問題がほぼ解決しました。
また、『第1種工場』から『第2種工場』へとエネルギー管理指定工場を変える事に成功しました。
参考:経済産業省 資源エネルギー庁「工場・事業場の省エネ法規制 事業者の義務」
ステップ2
ステップ1から約10年、生産量が増えてきたタイミングで、残っている非効率なコンプレッサーやドライヤー、その他設備の更新入替を行いました。
再度、図面作成や水量の確認、冷却塔など、コンプレッサーやドライヤー以外の細かい事にも目を配り、配管工事を含めた工事をさせていただきました。
結果、生産量が増えたにも関わらず、電気量-150kW削減することができ、導入前後も電気料金が格段に下がりました。